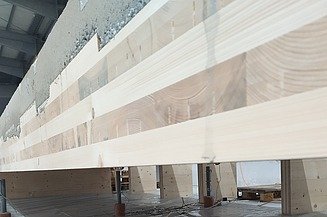
In addition to the usual method with subsequent in-situ concrete, the ZÜBLIN timber-concrete composite is also designed as a prefabricated system. In this way, the good properties of concrete in the compression zone as a vibration damper and as a mass provider for sound insulation are optimally combined with the dry, fast and precise construction method of timber construction. Fire resistance class REI 90 is also achieved in the visible version.
You plan
Our wood-concrete composite elements score points for your special requirements
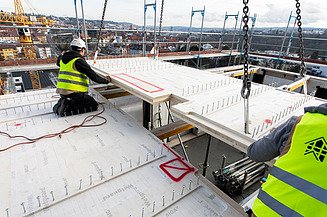
Your advantages
- High load-bearing capacity despite slim panels
- Significantly reduced dead weight compared to pure concrete slab
- Lower component thickness than with a pure wooden ceiling due to the omission of the gravel fill
- Reduced vibration behavior due to stiffening concrete surface
- Effective barrier against the spread of fire
- Better sound insulation (airborne and structure-borne sound) than wooden ceilings
- Short construction time thanks to factory-prepared LENO® elements
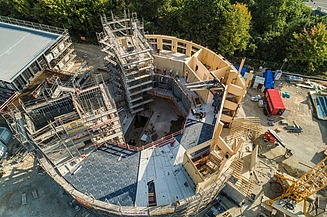
- Ceiling underside in wood look for higher living quality
- Simple connection of suspended components or installations/suspended ceilings
- Only edge formwork is required for concreting
- Optional cambering of the LENO® elements: no need to undercut the elements during the concreting process = significant reduction in construction time possible
- Reduction of CO2 emissioins by up to two thirds compared to a pure concrete ceiling
Unanswered questions?
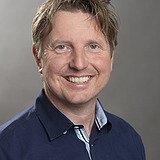
Our HBV elements have a lot to offer!
Click here for the technical product sheet:
German factsheet wood-concrete composite elements