News
Always up to date!
Discover what's happening in front of and behind the scenes at ZÜBLIN Timber. Innovative projects and insights from our timber construction sites, exciting news and highlights from our colleagues can also be found!
We are present at various events and functions. Need to talk? Then let's get going - let's network.
Lena Bachmeir
Marketing and Communications
Susanne Hörmann
Head of Marketing and Communications
Events and functions
Meeting | Where | When | Learn more |
Parliamentary symposium - Turnaround in construction policy | Berlin | 8.9.2025 | Info |
Association meeting of Hessian master carpenters | Bad Hersfeld | 12.+13.9.2025 | Info |
EASTWOOD 2025 | Leipzig | 18.+19.9.2025 | Info |
European Congress (EBH) | Cologne | 9.+10.10.2025 | Info |
Vocational information fair Rotary Club | Schrobenhausen | 11.10.2025 | Info |
Visit from VHS Aichach | Aichach | 16.10.2025 | Info |
Vocational information fair Schwäbisch Hall | Schwäbisch Hall | 18.10.2025 | Info |
Bavarian Carpentry and Timber Construction Trade Day | Würzburg | 24.+25.10.2025 | Info |
Vocational information fair Rotary Club | Aichach | 25.10.2025 | Info |
Baden-Württemberg timber construction conference | Stuttgart | 11.11.2025 | Info |
Forum Holzbau International | Innsbruck, AT | 3.+5.12.2025 | Info |
News & Latest news
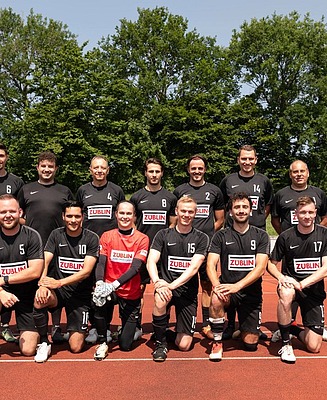
ZÜBLIN Cup 2025 in Stuttgart - woodchippers lift the trophy
Read more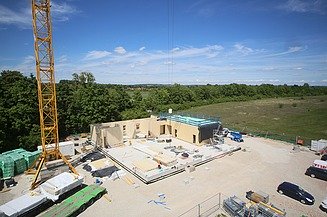
Start of timber construction at the Green Center in Landshut: A beacon for innovation - connecting people, developing ideas.
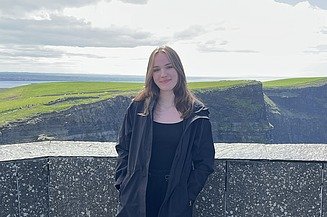
New horizons for trainees - Certificate Kaufmann:frau International
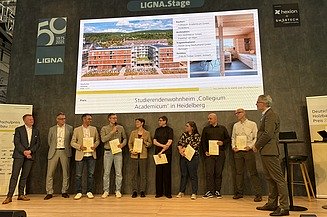
Award for the "Collegium Academicum in Heidelberg" project

Schule am Hang in Frankfurt celebrates topping-out ceremony
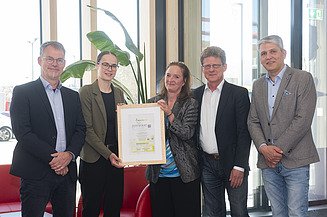
New T3 office building from ZÜBLIN Timber certified with wood from Hier®
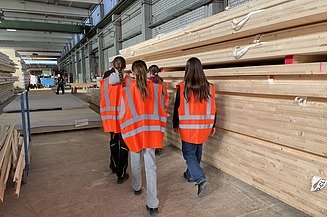
Girls's Day 2025 at ZÜBLIN Timber
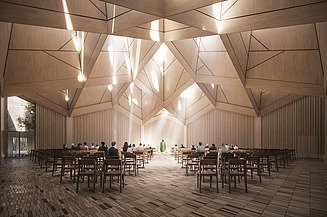